Critical battery minerals such as lithium, cobalt, nickel, and graphite are expected to face global shortages in the coming years as the number of electric vehicles (EVs) and battery energy storage systems grows rapidly. The situation is further complicated by the fact that the production of these minerals, particularly their refining into battery materials, is heavily concentrated in China, increasing supply risks in the current geopolitical landscape. Since ramping up mining production is challenging in the short term, attention is turning to battery recycling. In the longer term, by 2040, recycling is expected to meet about 10–30% of the battery industry’s raw material demand.
High expectations for recycling and market challenges
Despite high expectations for recycling, economic and political challenges hinder progress. The prices of battery minerals have remained low due to oversupply and lower-than-expected EV sales, particularly in Europe. This has made it difficult for new recycling industry players to compete, as recycled materials must compete with exceptionally cheap virgin raw materials.
In Europe, many battery factory projects have been delayed or canceled, reducing the amount of production waste available for recycling and weakening the business prospects of recycling operators. Additionally, a significant portion of European battery factories are owned by Chinese or Korean companies, which typically have their own recycling companies or established partnerships in Asia.
Investment needs and the black mass challenge
Investments in the recycling market are necessary to ensure sufficient capacity in Europe when large numbers of EV and hybrid batteries begin to reach end-of-life. Given the high number of electric vehicles and the large size of their batteries, this segment is crucial for the recycling market. Battery energy storage systems will also generate significant recycling volumes, and even the batteries used in smaller electric mobility devices require dedicated recycling solutions.
However, these investments depend on whether new players can secure contracts for recyclable materials (“feedstock”) and find buyers for their recycled materials. Estimates suggest that 44% of the announced battery recycling capacity in Europe is currently on hold or facing uncertainty regarding implementation.
Europe faces challenges regarding “black mass,” the intermediate product of battery recycling. Exporting black mass outside the OECD is not permitted, even though there is an oversupply in Europe and insufficient processing capacity. At the same time, China has low utilization rates at its battery recycling plants, meaning there is demand for European black mass. However, the EU aims to keep black mass in Europe to support its self-sufficiency in critical materials.
Impact of new regulations and benefits of recycling
The EU has been proactive in regulating battery and raw material recycling. The Battery Regulation (2023) and the Critical Raw Materials Act (CRMA, 2024) set strict requirements for recycling and material recovery. According to the Battery Regulation, at least 65% of lithium-ion batteries must be recycled by 2026, increasing to 70% from 2031. Additionally, new batteries must include a minimum amount of recycled raw materials, such as 6% recycled lithium by 2031 and 12% by 2036.
Currently, about 80% of recycling materials for the battery industry come from production scrap at battery factories. This trend will continue, as recycling volumes from EVs and plug-in hybrids are expected to rise significantly only around 2035. Recycling could reduce energy consumption by up to 75% and water consumption by 80% compared to traditional mining and refining. However, challenges remain in terms of expertise, technology, and financing.
Balancing regulation and future prospects
The EU’s ambitious regulatory efforts pose challenges for companies. Critical raw materials are regulated not only by battery and raw material laws but also by other legislation, such as regulations on waste electrical and electronic equipment (WEEE) and end-of-life vehicles (ELV). The workload caused by these regulations has been acknowledged in the new European Commission’s agenda.
When drafting Finland’s national battery strategy in the fall of 2020, companies advocated for strict requirements for the European battery industry, seeing them as a way to improve competitiveness. Time will tell whether these expectations were met.
A major challenge for regulation is the rapid evolution of battery technology. When the Battery Regulation was being drafted, the market share of lithium iron phosphate (LFP) batteries in Europe appeared to be growing slowly. However, the rise of large-scale battery energy storage systems and the wider adoption of LFP batteries in the EV industry have changed the situation rapidly. Maintaining technological neutrality should remain a key goal.
Final thoughts from the guest columnist
European battery recycling needs clear and long-term regulations that do not impose an unreasonable burden on businesses. Policymakers and regulators must act wisely and cautiously to ensure that regulations remain practical and that targets are not raised like bids in an auction. For regulations to be credible, their goals must be realistic and achievable. The relative competitiveness of recycled materials must be promoted through both incentives and regulatory measures, as the existing system is unlikely to relinquish its established position easily.
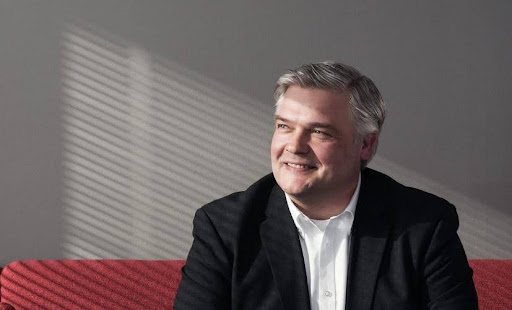
Jarkko Vesa is an expert in critical minerals and battery markets with extensive experience in strategic consulting and market analysis. He coordinated Finland’s battery strategy and has conducted background research on critical mineral supply for organizations such as the IEA through his company, Not Innovated Here.
Jarkko’s popular LinkedIn groups, Critical Materials and Battery Strategy 2030, have attracted thousands of active followers. Follow them and join the discussion!